Scraped Surface Heat Exchangers
OVERVIEW
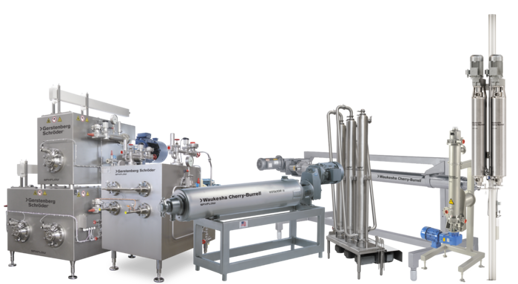
Our scraped surface heat exchangers (SSHEs) are designed for handling viscous or fouling fluids, such as those in the food, pharmaceutical, and petrochemical industries. A rotating scraper or blade continuously removes deposits from the heat transfer surface, which offers several benefits compared to conventional heat exchangers:
- Improved Heat Transfer Efficiency: SSHEs help prevent fouling or scaling on the heat transfer surface by constantly scraping off the accumulated deposits. This maintains a clean surface for heat transfer, resulting in higher overall heat transfer efficiency and reduced fouling-related heat transfer resistance. This means that an SSHE can maintain its heat transfer performance for longer periods without frequent cleaning, reducing downtime and increasing process efficiency.
- Enhanced Product Quality: In industries where product quality is critical, such as food and pharmaceuticals, SSHEs can provide significant benefits. The continuous scraping action helps to prevent product buildup on the heat transfer surface, minimizing the risk of product degradation, fouling, or contamination. This results in improved product quality, consistency, and purity, making SSHEs ideal for processing sensitive or high-value products.
- Increased Process Flexibility: SSHEs are versatile and can handle a wide range of process fluids, including viscous, particulate-laden, and fouling-prone fluids. They are also capable of handling a wide range of operating conditions, including high temperatures and pressures. This makes SSHEs suitable for a variety of applications, from heating or cooling viscous food products, such as sauces and confectionery, to processing petrochemicals, pharmaceuticals, and specialty chemicals.
- Reduced Maintenance and Downtime: Fouling is a common issue in heat exchangers, and it can lead to decreased heat transfer efficiency, increased energy consumption, and increased maintenance and downtime. SSHEs with their built-in scraping action can help reduce fouling, which in turn reduces the need for frequent cleaning and maintenance, leading to decreased downtime and increased productivity. This can result in significant cost savings and improved process reliability.
- Energy Savings: Fouling on heat transfer surfaces can increase the energy requirements for heating or cooling processes, as it reduces the effective heat transfer area and increases the temperature difference across the exchanger. By minimizing fouling, SSHEs can help reduce energy consumption and operating costs, making them more energy-efficient compared to conventional heat exchangers.
- Compact Design: SSHEs are often designed to be compact, which means they can be easily integrated into existing process lines or systems without requiring extensive modifications. This makes them ideal for retrofitting into existing processes where space is limited.
SPARE / REPLACEMENT PARTS
Why Select Genuine Spart Parts for Your Scraped Surface Heat Exchanger
Because Downtime is the Enemy of Efficiency
Some scraped surface heat exchanger replacement parts may seem attractive due to a low price, but only looking at the initial cost may leave you vulnerable to unforeseen costs later. There are reasons that alternative, “might fit” parts cost less, including the possible use of lower quality materials or modifying important manufacturing steps, such as polishing or coating. This could result in a part not lasting as long.
For some applications, this might not matter if the user does not mind making frequent replacements. But for scraped surface heat exchanger applications such as in the food or pharmaceutical industries, polishing and coating are critical to sanitary performance and cleanability. A lower quality finish on a part could increase the risk of bacterial growth and contamination of the final product.
Why Use Genuine Spare Spares in Your Scraped Surface Heat Exchanger
If you install a third-party aftermarket scraped surface heat exchanger part into your original scraped surface heat exchanger, this will void your scraped surface heat exchanger’s warranty. That’s because all our parts are engineered to work seamlessly within the process functions they were designed for. High precision means high efficiency. Even the tiniest bit of lag or play can impact your scraped surface heat exchanger’s efficiency, become a potential safety hazard for your employees, or cause a process line to go down until a proper replacement part is ordered and installed.
How to Get Genuine Spare / Replacement Scraped Surface Heat Exchanger Parts
Our global partner network means the scraped surface heat exchanger replacement parts you need to stay up and running are readily available. And in the event you require expert installation, our partners are fully trained and ready to help at a moment’s notice.
Why Genuine Spare / Replacement Scraped Surface Heat Exchanger Parts Are Key
Safety is our top priority at SPX FLOW, which is why all our scraped surface heat exchanger replacement parts endure rigorous testing and comply with legal requirements.. This commitment to safety translates to scraped surface heat exchanger spare parts we stand behind. Can the same be said for third-party valve replacement parts?
No amount of downtime and certainly no potential safety hazard is worth saving a few bucks on a “might fit” part in the short term.
Don’t take unnecessary risk. Order genuine OEM scraped surface heat exchanger replacement parts today, and rest assured you made the right decision.